Noticias
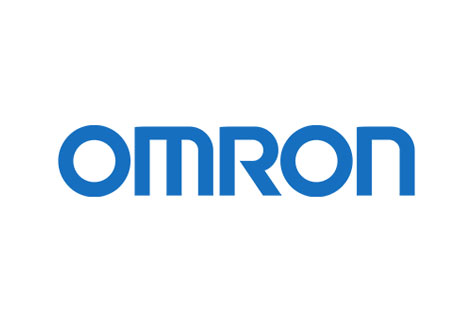
Cuatro casos de uso demuestran cómo la información en tiempo real sobre los activos minimiza el tiempo de producción.
El tiempo de inactividad de la máquina no planificado es un gran dolor de cabeza para el sector empresarial. En 2016, Aberdeen Group descubrió que estos eventos les cuestan a las empresas un promedio de $260,000 USD por hora, un aumento del 60% con respecto a su encuesta de 2014. Si bien Aberdeen no ha publicado más actualizaciones, parece probable que los problemas en curso, incluidos los puntos débiles como el envejecimiento de la infraestructura, la escasez de trabajadores calificados y las recientes interrupciones sociales, continúen aumentando los costos operativos al reducir la disponibilidad de equipos.
En la fabricación, los operadores de la planta están abordando el tiempo de inactividad no planificado de la máquina al migrar del mantenimiento preventivo al mantenimiento predictivo. A diferencia del mantenimiento preventivo que se realiza de acuerdo con un programa que refleja eventos históricos, el mantenimiento predictivo monitorea la condición de los activos en tiempo real y notifica al usuario antes de que las fallas interrumpan la producción. Los avances en sensores, análisis y tecnologías de la comuni- cación hacen que el mantenimiento predictivo sea cada vez más práctico y accesible para las pequeñas, medianas y grandes empresas de fabricación.
Este documento técnico analiza las formas en que una sólida estrategia de mantenimiento predictivo respaldada por tecnologías de vanguardia puede ayudar a los fabricantes a adelantarse a los problemas de los equipos y minimizar el tiempo de inactividad. Se proporcionan cuatro casos de uso para guiar a los tomadores de decisiones y definir los esfuerzos de trabajo y los presupuestos.
Supervisión en línea e inteligencia artificial para optimizar la eficiencia
Si bien el mantenimiento predictivo puede parecer desconocido, la estrategia en realidad emplea metodologías bien entendidas para replicar los análisis de ingenieros de mantenimiento capacitados. Una vez que estos análisis se ingresan en un algoritmo, las soluciones de mantenimiento predictivo utilizan software de inteligencia artificial (IA) para monitorear los activos y generar alertas cuando se detectan condiciones inusuales, como vibraciones anormales o altas temperaturas.
Agregar sensores a equipos clave y acumular datos sobre su desempeño proporciona beneficios inmediatos y a largo plazo. Los operadores de la planta pueden eliminar las actividades de inspección y mantenimiento que requieren mucho tiempo, minimizar los defectos de calidad y fortalecer las medidas de seguridad y protección. En última instancia, cualquier conocimiento derivado de los datos permitirá a los fabricantes correlacionar el comportamiento de la máquina con los eventos en la fábrica. Este análisis ayuda a las empresas a maximizar la eficiencia en un mercado cada vez más competitivo.
Desarrollar un plan que ofrezca resultados significativos en menos tiempo
Si existe un obstáculo para implementar el mantenimiento predictivo, es la conectividad de los equipos. Como señala una encuesta reciente, hasta el 92% de las máquinas instaladas no están diseñadas para la conectividad.
Es comprensible que los fabricantes se muestren negados a abandonar estas inversiones, razón por la cual están recurriendo a soluciones adaptadas como una forma de modernizarse manteniendo los costos accesibles. Los proveedores de la industria ya han introducido varias soluciones tecnológicas en el mercado para actualizar los equipos instalados con poca o ninguna modificación.
Los programas de reacondicionamiento suelen comenzar priorizando la base instalada. La priorización permite a los fabricantes centrarse inicialmente en los equipos que requieren un mantenimiento más frecuente y tienen el mayor impacto en la producción. Una vez identificados los activos críticos, la implementación de la solución de mantenimiento predictivo es sencilla. Los pasos clave incluyen replicar el conocimiento de los ingenieros para el objetivo activo, establecer una línea de base de condiciones aceptables, adaptar uno o más sensores a la máquina y establecer umbrales de advertencia y alarma.
Caso 1: Monitoreo del estado del motor eléctrico.
Los componentes desgastados constituyen una de las principales causas de falla del motor eléctrico trifásico. OMRON ayudó recientemente a una empresa de bebidas a encontrar una solución eficáz para reducir estos eventos de falla. Antes de la implementación de la solución, la empresa inspeccionaba manualmente los motores de su línea de embotellado en intervalos de tres y seis meses y revisaba los motores una vez al año. Con esta estrategia de mantenimiento preventivo, los trabajadores reemplazaban piezas con frecuencia, pero este enfoque era costoso y no logró eliminar el tiempo de inactividad no planificado.
El S8VK-X realiza un seguimiento del voltaje de salida de CC, la corriente, la corriente máxima y el tiempo de ejecución de forma remota para identificar rápidamente cualquier anomalía del circuito de CC y maximizar el ciclo de vida.
La modernización del motor con un transformador de corriente permitió a un dispositivo de monitoreo predictivo ejecutar un análisis de distorsión en tiempo real, detectar anomalías y analizar el modo de falla. Con esta información, la empresa pudo eliminar las inspecciones que consumían mucho tiempo y confiar en las alertas que indicaban un requisito de servicio. La transición a una solución de mantenimiento predictivo ha demostrado reducir los costos y agilizar el trabajo de mantenimiento, al mismo tiempo que mejora la calidad del producto al detectar fallas en las juntas de goma antes de que materias extrañas puedan contaminar los productos. La compañía planea implementar la solución en otras instalaciones y cambiar algunas prácticas de mantenimiento existentes.
Caso 2: Monitoreo del estado de la bomba de recirculación.
Las bombas de recirculación industriales funcionan casi continuamente. Un fabricante de semiconductores utilizó inspecciones manuales para revisar un motor de tratamiento de agua en su planta, pero realizar inspecciones precisas fue difícil sin apagar la bomba. La programación del mantenimiento siempre fue un desafío debido a las continuas necesidades de producción. Esto significaba que el servicio podría realizarse demasiado pronto (pérdida de tiempo y materiales) o demasiado tarde (después de que una falla inesperada afectara la producción).
La actualización de la bomba de recirculación con un sensor de vibración permitió que el dispositivo de monitoreo midiera las vibraciones de alta frecuencia, detectara anomalías y analizara el modo de falla. Las alertas permiten a los ingenieros de mantenimiento monitorear el estado de la bomba de forma remota, juzgar el impacto potencial de las anomalías y resolver problemas sin estar en el sitio. Este caso de uso muestra cómo una solución de mantenimiento predictivo puede agilizar el trabajo de mantenimiento y al mismo tiempo respaldar la producción de semiconductores al evitar tiempos de inactividad no planificados.
Caso 3: Monitoreo del estado del sistema hidráulico.
Las válvulas hidráulicas son esenciales para el funcionamiento normal de muchas máquinas industriales, y los aumentos de temperatura a menudo generan la contaminación de desechos en el fluido hidráulico que fluye a través de las válvulas. Cuando un fabricante de automóviles líder confiaba en las inspecciones térmicas manuales para monitorear el estado de las válvulas en sus prensas hidráulicas de panel de la carrocería, a veces ocurría un tiempo de inactividad no planificado que duraba días o semanas. Esto se debió al hecho de que los ingenieros de mantenimiento no pudieron monitorear continuamente la temperatura de la válvula.
La modernización de prensas con sensores de imagen térmica permite que el dispositivo de monitoreo mida continuamente la temperatura de la válvula, detecte anormalidades y analice el modo de falla. Los aumentos en la temperatura de la superficie generan alertas automáticas que permiten al personal de mantenimiento tomar medidas inmediatas si es necesario. Esta solución de mantenimiento predictivo redujo las necesidades generales de mantenimiento y mejoró la disponibilidad de la máquina. Además, dado que la empresa ya no necesitaba trasladar la producción a otras prensas hidráulicas, la eficiencia mejoró y los costos, como el pago de horas extra, bajaron.
Caso 4: Fuente de alimentación con supervisión integrada.
Los grandes entornos de producción suelen albergar cientos de paneles de control. Los aumentos de temperatura en la fuente de alimentación del panel de control a menudo indican que estos componentes se están degradando. Los ingenieros de mantenimiento de un fabricante de automóviles utilizaban voltímetros digitales para comprobar las fuentes de alimentación en busca de condiciones fuera de las especificaciones. Estas inspecciones manuales tomaban mucho tiempo y eran imprecisas, ya que los componentes a veces se degradaban entre inspecciones. Para limitar el tiempo de inactividad, estos trabajadores se basaron en programas preventivos para reemplazar las fuentes de alimentación independientemente del estado del dispositivo.
La modernización de los paneles de control con fuentes de alimentación inteligentes ha llevado la funcionalidad de IA a la fábrica. Con sensores de temperatura, voltaje y potencia, cada fuente de alimentación puede calcular su propio ciclo de vida y enviar su información en tiempo real a una pantalla incorporada. La red integrada también admite la supervisión remota de varias fuentes de alimentación desde una ubicación central. El uso de dispositivos inteligentes como parte de una solución de mantenimiento predictivo proporciona un marco para construir un entorno de IoT. Permite un control intensivo sin inspecciones prácticas, lo que mejora la eficiencia y la disponibilidad del equipo al mismo tiempo que reduce los costos.
Mantenimiento Preventivo vs. Mantenimiento Predictivo
Los fabricantes que emplean estrategias tradicionales de mantenimiento preventivo a menudo se encuentran perdiendo señales clave de falla que ocurren entre inspecciones o reemplazando prematuramente el equipo para evitar estas fallas potenciales. Estos problemas se generan principalmente por la falta de monitoreo 24/7 de equipos críticos. Al migrar a una estrategia de mantenimiento predictivo, los fabricantes pueden estar seguros de que su equipo está siendo monitoreado las 24 horas del día y que el análisis de datos en tiempo real revelará cualquier problema potencial mucho antes de una falla real. Esto minimiza el tiempo de inactividad y al mismo tiempo reduce drásticamente los costos generales.
Otros artículos de interés
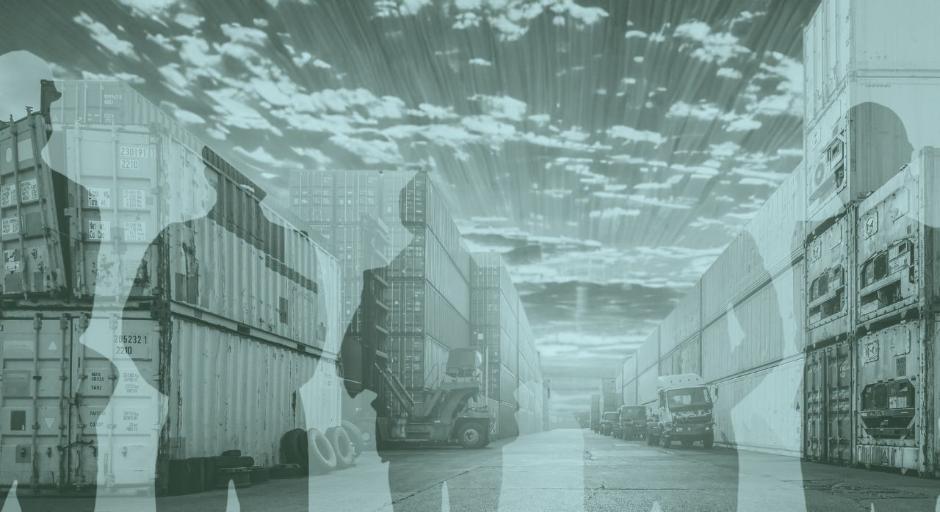
Ante aranceles, ¿qué papel juegan los organismos bilaterales?
La presión política sobre el comercio internacional ha incrementado de manera notable

La digitalización en mantenimiento reduce fallas en planta
En la industria actual, mantener las máquinas en funcionamiento no basta. La transformación
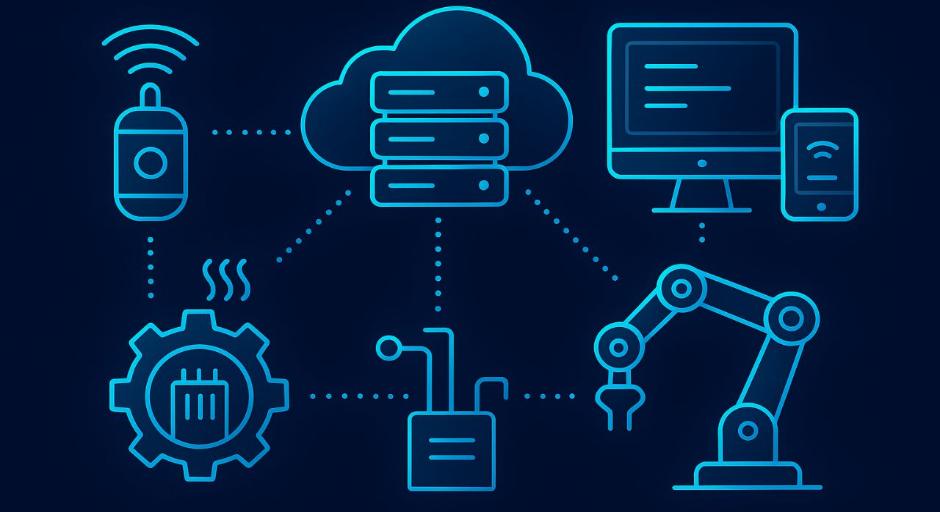
Se transforma la seguridad industrial con tecnología inteligente
La seguridad en las plantas industriales mexicanas ha vivido una transformación impulsada
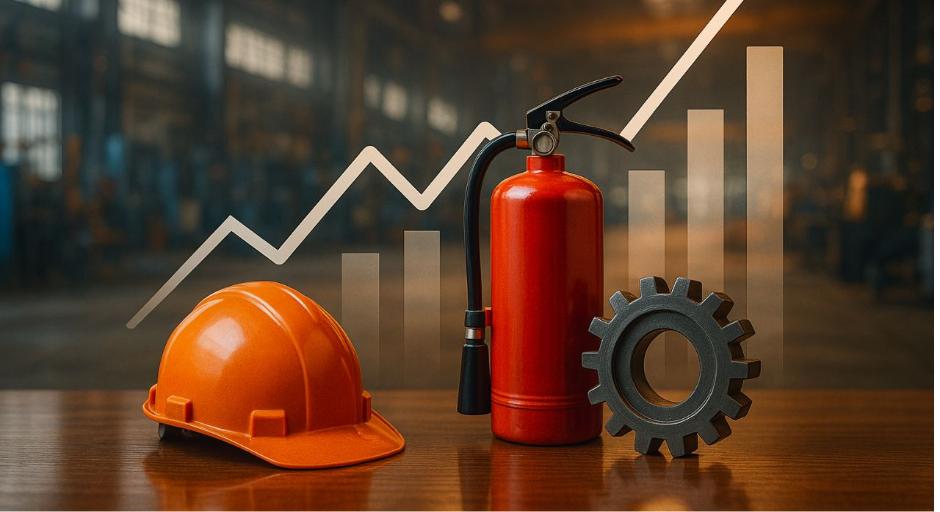
La seguridad industrial tiene un valor estratégico
La seguridad industrial es, y deb ser vista, como un componente estratégico
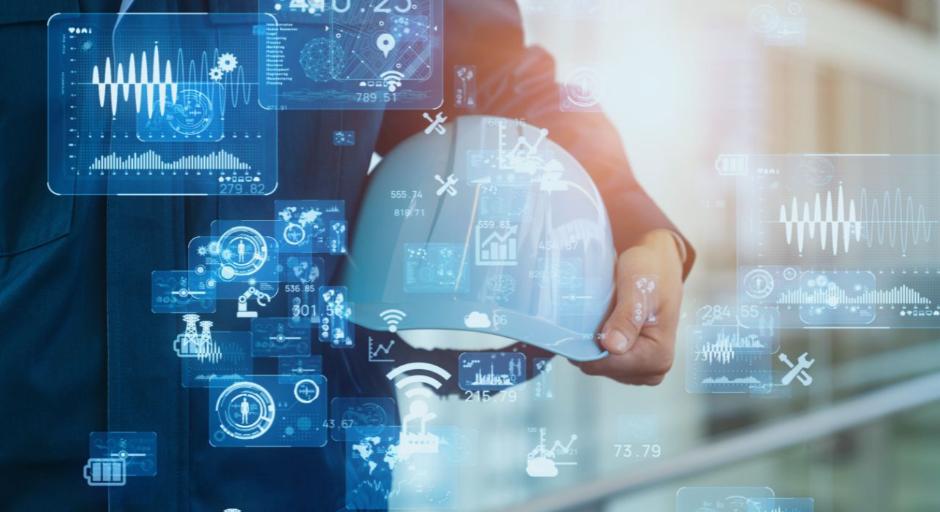
Impulsa software productividad industrial
La digitalización ha adquirido un papel estratégico en la industria energética y
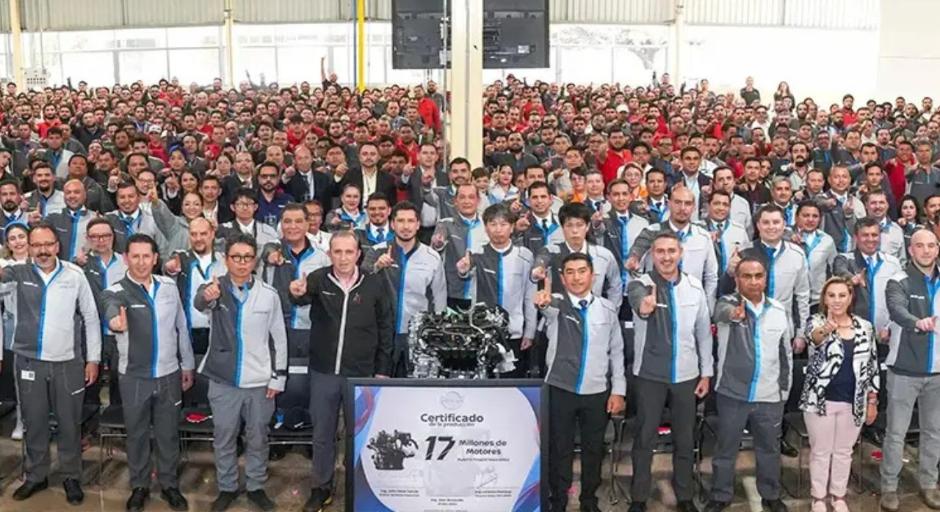
Alcanza Nissan los 17 millones de motores
La planta Powertrain de Nissan en Aguascalientes alcanzó un nuevo hito en